

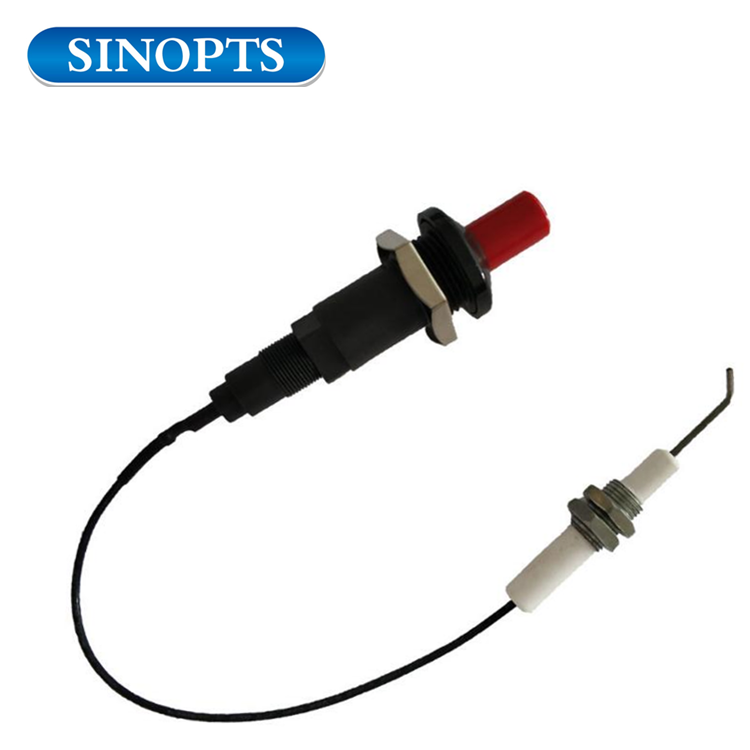
The experiment was performed using two PEs, one as an emitter transducer and another as a receiver, for sending and receiving ultrasonic pulse waves (405 kHz), on silica aerogels 10-cm wide where, aerogels undoubtedly come under a class of fascinating materials having high porosity, low density, low thermal conductivity, large surface area, transparency in the visible range, and many more peculiar properties for scientific and industrial uses. authors in found a positive relationship between longitudinal and transverse velocity with temperature. The relationship between the relative velocity ∆ v/ v of sound in a single crystal YBazCu307 to temperature is non-linear. Thus, most ultrasonic creep tests have utilized PVDF recently. These potential properties and their flexibility in use are very difficult to find in many available sensors or smart materials. In another report, PVDF of 4 mm diameter with hosing diameter range of 8 mm to 20 mm was used, which can sense loads with frequency ranging from 0.001 GHz to 2 GHz. In addition, the PVDF can be used in a wide temperature range (−40 ☌ to +160 ☌). The PVDF used can sense very small vibrations from 1 Hz to 20 Hz, slight changes in stress, after more than 10 years and 100 million pressure cycles at a pressure range from 10 kPa to 2 MPa, with approximately 10% accuracy, and about 1 ms response time. This test was used as one of many stages in an experimental program to test the creep in polymers and thin-film of piezoelectric polymer made from polyvinylidene fluoride (PVDF). Vibrocreep in polymers means an acceleration of creep through the specimen to the cyclic loading regime. Using Piezoelectricity to Calculate Solid-Material Properties The purposes of this research are: (a) to summarize published articles that involve PE applications in testing material properties (b) to report recent progress in this field and (c) to establish a guideline for the frequency levels or ranges of PE use associated with the dimensions of test specimens for these types of tests. There are many advantages of PEs which are very important in mechanical tests such as (1) the high electromechanical transformation efficiency (2) a broad range of characteristics can be achieved with different material compositions (high degree of freedom in characteristics design) (3) high stability and (4) their suitability for mass production and economic production. It is also reciprocal, so that if the crystal is exposed to an electric field, it will experience an elastic strain causing its length to increase or decrease according to the field polarity. The effect is practically linear, i.e., the polarization varies directly with the applied stress, and is direction-dependent, so that compressive and tensile stresses will generate electric fields and hence voltages of opposite polarity. A stress (tensile or compressive) applied to such a crystal will alter the separation between the positive and negative charge sites in each elementary cell leading to a net polarization at the crystal surface. A crystal exhibits the piezoelectric effect if its structure has no center of symmetry. In contrast, the reverse piezoelectric effect causes the crystal to produce vibration when it is placed in an electric field. The piezoelectric effect causes a crystal to produce an electrical potential when it is subjected to mechanical vibration. The mechanical wave or vibration is generated through passing an electric wave through the two electrodes of the PE then, into the material of PE itself. The classical definition of PE is a polarizing ceramic material that can convert mechanical energy to electric energy and vice versa. The role of piezoelectric elements (PEs) in ultrasonic tests and smart system applications is becoming increasingly difficult to ignore, especially with regard to art using PE in finding the mechanical properties of solid materials.
